Sustainability
Social (S):Improving Quality
Improving Quality
Basic Approach
Under our calling of “Going ahead with you,” stated in the Nitta Group Mission, we strive to provide high-quality products and services.
NITTA Group Quality Policy
In order to provide high-quality products and services, the Nitta Group works with customers to advance product development and to create products that take safety and the environment into consideration.
Promotion Structure for Quality Improvement Activities
The Nitta Group has created a structure to promote quality management, headed by the Nitta Corporation representative director/president. We have established a QMS Conference under a general management supervisor, with the Safety, Environment, and Quality Department supervising and promoting quality improvement activities.
We perform organizational management in divisions and group companies through the Quality Control Committee. Our domestic and overseas manufacturing sites have acquired ISO 9001 certification (IATF 16949 certification for automobile parts manufacturing sites), the international standard for quality management systems. We are building mechanisms for quality control based on the requirements of standards.
Quality Education Activities
The Nitta Group carries out TQM activities, of which QC circle activities are a part. Drawing on concepts of the Toyota Production System, in production sections we carry out NS own study and other autonomous activities by which employees think and make improvements on their own. In support sections we promote “own process completion” centered on improvement of work tasks.
Moreover, the Safety, Environment, and Quality Department, which oversees the Nitta Group, systematically conducts quality patrols aimed at quality improvement at manufacturing sites and group companies, with the aim of improving the quality level overall.
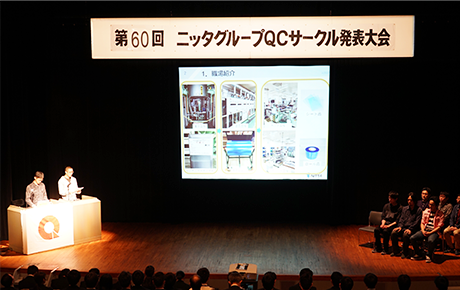
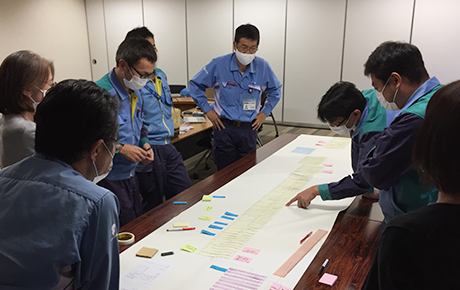
「Total Nitta System」
Untiring pursuit of improvement of Q (quality), C (cost), and D (delivery time)
-
TQM (Total Quality Management)
activitiesReporting sessions/guidance sessions for managers
-
- ・Optimization of management issues
-
QC circle activities
Site-led quality improvement activities
-
- ・Activation of workplace communication
- ・Formation of logical thinking
-
NS (Nitta System) own study
Pursuit of efficient mechanisms
-
- ・Pursuit of one man-hour
- ・Elimination of “7 wastes”
- ・Construction of mechanisms for standardization
-
Autonomous activities
Activities to activate management issues from on-site perspectives
-
- ・Creation of a workplace culture in which people operate a small PDCA cycle to think and make improvements on their own
- ・Sharing of high-level policies
-
Own process completion (JKK) activities
Efforts to improve work efficiency in support sections
-
- ・Elimination of work dependent on individuals
- ・Elimination of unnecessary work
- ・Standardization
-
5S activities
Five elements as the foundation for improving work environments
-
- ・Improvement of work efficiency through comfortable environments
- ・Mutual checks and ongoing implementation
Quality Education
As part of our education and training on quality, the Safety, Environment, and Quality Group sets a clear schedule for the education and training program every year, then rolls out the schedule to all sections and implements it systematically. In all divisions and group companies, we perform policy management and development in response to top-level policy.
Furthermore, to achieve sectional quality goals, each section writes individual quality goals on a policy card every year to boost employee awareness, and works to achieve these goals.
In this way, the Nitta Group operates a quality management system and engages in quality control activities throughout the organization.