Sustainability
Occupational Safety and Health
Occupational Safety and Health
Basic Approach
The Nitta Group effectively operates management systems integrated with its business activities, and, while working to effect continuous improvements and achieve objectives and goals, complies with relevant laws and other requirements.
NITTA Group Occupational Safety and Health Policy
- ・Achievement of zero-risk workplaces
- We will make occupational safety and health risks clear and will continuously effect improvements to create zero-risk workplaces.
- ・Acting under the recognition that placing safety first and ensuring the health and safety of all employees is the highest priority and the foundation for our corporate activities, we will comply with Japan’s Industrial Safety and Health Act and other regulations and rules. At the same time, through safety and health activities, we will engage in ongoing improvement and work to prevent and eliminate occupational accidents, automobile accidents, and deterioration of the health environment in the company.
Under the above policy, we have established and operate 10 Safety Articles and 10 Pledges for Safe Behavior.
Promotion Structure
Ensuring the health and safety of everyone working at the Nitta Group is our top priority and is recognized as the foundation of our corporate activities. We have established a safety promotion system with our company president as the chief officer. The Nitta Group Safety and Health Committee, composed of executives from each group company, the Safety and Health Promotion Officers Conference, composed of promotion managers from each company, the Safety and Health Committee at sites, composed of managers from each business division and representatives of the union, and the Workplace safety and health meetings at sites, composed of units at the workplace level, hold monthly meetings at each level to share and implement various initiatives aimed at risk reduction. In particular, we emphasize the participation of working people, and all employees work together to continuously improve the workplace environment and strive to create a comfortable workplace.
Preventing Occupational Accidents
In order to create workplaces that ensure safety and health for all workers in the Nitta Group, we do risk assessments to identify occupational safety and health risks and mitigate and eliminate any dangers or hazards. We also carry out various patrols to identify further overlooked risks and any flaws in risk countermeasures. These activities are all aimed at achieving zero-risk workplaces.
We provide in-house education to boost employees’ safety awareness, including education for new employees and for foremen. Our seminars also cover topics such as heat stroke prevention, traffic safety, risk assessment of chemicals, and protective equipment management.
In addition, to help employees better detect hazard risks, we hold training sessions as needed, where safety and health promotion managers act as trainers and use risk experience devices that encourage broader experiences and improve sensitivity to risk. Through systems like these, we are working company-wide to prevent workplace accidents.
--- Initiatives to achieve a zero-risk workplace ---
Item | Details |
---|---|
Risk assessments | Employees certified as having the necessary skills conduct risk assessments. They identify potential workplace risks and study ways to deal with them, with the highest risks given priority. Risk assessments are held once a year as well as in the event of a disaster to ensure that no risks have been overlooked. The results of risk assessments and countermeasures are compiled and confirmed at each Nitta Group company and division. The Safety Department then compiles all the results and countermeasures from across the Nitta Group and provides guidance if any flaws are found. Under a philosophy of “Blame the system and not people,” we aim to eliminate all potential risks through management measures, fundamental measures that do not rely on protective equipment, and engineering-based measures. |
Risk reduction in the event of a disaster | We have introduced disaster simulation training, and we draw up disaster response action plans based on simulations. We formulate action plans for each time period, starting from immediately after the disaster occurs. Every year we repeat this cycle of training, revising the action plan, and training to strengthen our disaster response capabilities. The aim is to minimize risks in the event of a large-scale disaster. |
Emergency drills | In order to deal with emergencies, particularly those with high risk such as chemical spills, we formulate response procedures in anticipation of such an emergency and carry out drills every year. |
Patrols by top management | The top management team conducts on-site patrols, focusing on workplaces that have experienced an accident over the past year and giving guidance for improvement. |
Patrols by the Safety Department | Patrols are held once a month by the Safety Department and the safety and health promotion managers of each workplace. They check workplaces where measures have been taken based on the results of risk assessments. If there are any flaws or need for improvement, they urge further remediation and provide follow-up until this is completed. |
Safety and health patrols | Besides regular patrols at each workplace, semiannual patrols are carried out by safety and health promotion managers, health managers, and union representatives. |
Patrols to prevent recurrence | The Safety Department checks workplaces that have suffered accidents and confirms whether recurrence prevention measures are working. If they are found to be ineffective, the Safety Department instructs the workplace to review those measures. |
Equipment safety checks | When introducing new equipment, its safety is checked before it goes into operation. The aim is to eliminate any potential risks associated with the introduction of new equipment and prevent accidents. |
Working environment measurements | Twice a year, we survey and analyze workplaces that handle or are exposed to hazardous substances. If any workplace is found to fall under Category 2 or 3, we study and put in place countermeasures with the aim of 100% improvement. |
Safe driving classes | Classes are held twice a year for drivers of company cars and employees who drive to work. Accident risks are shared through examples of accidents involving Nitta workers in order to raise awareness of driving safety. |
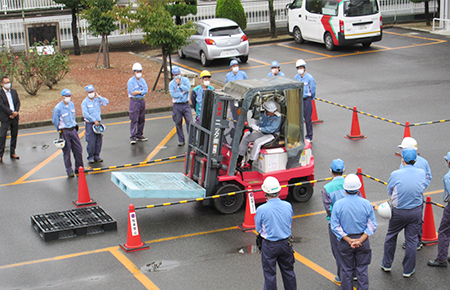
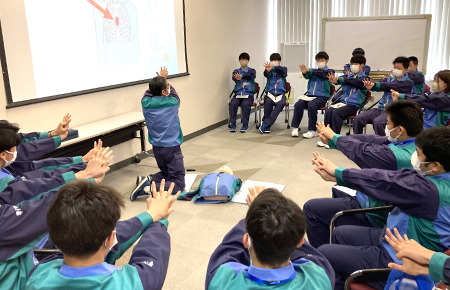
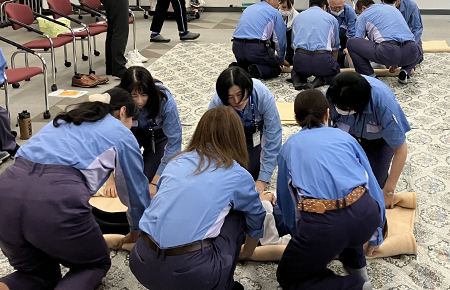
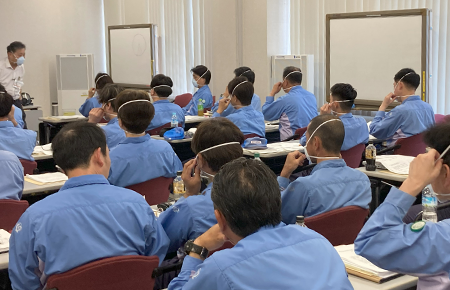